Cambridge Healthtech Instituteの第8回年次
Intensified and Continuous Processing
強化処理・連続処理
Process Intensification and Digitalisation Towards a Sustainable Future
持続可能な未来に向けたプロセス強化とデジタル化
2025年3月19日 - 20日 CET(中央ヨーロッパ標準時)
3月19日(水)
10:30Registration Open
PLENARY KEYNOTE: ADAPTING TO GLOBAL DEMANDS AND EVOLVING PIPELINES
プレナリー基調講演:世界的な需要への適応と進化するパイプライン
CMC Strategies for Diverse Pipelines and Complex Modalities
Christian Hunzinger, PhD, Senior Director and Head, CMC Development Proteins, ADCs and Chemical Entities, BioNTech
Biopharmaceutical treatment paradigms are shifting from monotherapy towards multi-target approaches with complex multimodal entities. This complexity also translates into increasingly complex CMC development and manufacturing strategies. The talk will provide a general overview on recent developments, challenges, and opportunities, along with examples from various stages of the CMC development lifecycle.
Enhancing Process Development: Balancing Yields with Downstream Efficiency and Emerging Technologies
Oliver Kaltenbrunner, PhD, Scientific Director, Process Development, Amgen Inc.
Explore the evolving landscape of process development, emphasising the critical balance between maximising yields and optimising downstream processing. This presentation will delve into the impact of upstream processes on primary recovery, integrating cutting-edge technologies like Process Analytical Technology (PAT), advanced modelling, and artificial intelligence. Supported by real-world examples, we'll examine how these innovations are reshaping process efficiency and performance in the industry.
12:20Session Break
12:30Sponsored Presentation (Opportunity Available)
13:00Networking Lunch in the Exhibit Hall with Poster Viewing

PROCESS INTENSIFICATION, KNOWLEDGE MANAGEMENT, AND CONTROL
プロセス強化、ナレッジマネジメント、制御
Integrated and Continuous Processing
Lara Fernandez-Cerezo, PhD, Associate Principal Scientist, Merck Sharp Dohme (MSD)
Merck & Co. Inc., Rahway, NJ, USA, is exploring the use of a Process Knowledge Management (PKM) tool to streamline technology transfers, aiming to address issues of duplication and enhance standardisation in the process. The PKM tool encompasses process calculations, automation, and documentation depository capabilities, and has demonstrated successful performance in a biological continuous manufacturing process case study. Merck & Co. Inc., Rahway, NJ, USA, is considering implementing PKM at an enterprise level, with plans to expand its use beyond biologics. The anticipated outcomes include optimising resource utilisation, automating data workflows with existing infrastructure, and revolutionising technology transfers.
Advancing Clinical Manufacturing through Novel PAT Tools for Biologics
Michael H. Olma, PhD, Supervisor GMP Advanced Analytics, Biologics Analytical R&D, MSD Werthenstein BioPharma GmbH
At our clinical manufacturing site here in Switzerland, we introduced novel Process Analytical Technologies (PAT) for Biologics. For this, we successfully established a variety of PAT tools in a GMP compliant way for upstream and downstream processing, for example Endress+Hauser Rxn4 and Repligen FlowVPX. This allows us to deploy advanced process control strategies and to support improved manufacturing processes. We would like to present our experiences with these tools.
Sustainability and Process Intensification Strategies at Novartis
Johanna Rapp, Senior Expert, DSP, Novartis
To achieve ambitious goals in reducing global warming, it is crucial to couple deliberate actions with a resolute mindset of stubborn optimism. At Novartis, we embrace this powerful combination as we strive to make a tangible impact through driving sustainable initiatives, including the design of resource-saving manufacturing processes. In this presentation, we will showcase process improvements that not only drive efficiency but also yield remarkable reductions in carbon emissions.
16:20Refreshment Break in the Exhibit Hall with Poster Viewing

CONTINUOUS PROCESSING: STATE-OF-THE-ART TECHNOLOGIES AND ECONOMIC VALUE
連続処理:最先端テクノロジーと経済的価値
State-of-the-Art Technologies in Continuous Processing
Richard D. Braatz, PhD, Edwin R. Gilliland Professor, Massachusetts Institute of Technology
This presentation describes upstream, downstream, and formulation technologies for continuous processing with experimental results presented for monoclonal antibodies, gene therapies, and viral, mRNA, and subunit protein vaccines.
A Techno-Economic Perspective on Continuous Bioprocessing: Is It Really Worth It?
Tommas De Santis, Institute of Bioprocess Science and Engineering, BOKU
This presentation explores the techno-economic viability of continuous bioprocessing, comparing it with batch processes in terms of cost-efficiency, scalability, and technological readiness. Through examining recent advancements and economic analyses, it evaluates whether the benefits, such as increased yield and reduced downtime, justify the initial high investment. The study aims to provide a clear economic perspective to aid in decision-making for adopting continuous bioprocessing in pharmaceutical manufacturing.
INTERACTIVE BREAKOUT DISCUSSIONS
インタラクティブブレイクアウトディスカッション
Interactive Breakout Discussions are informal, moderated discussions, allowing participants to exchange ideas and experiences and develop future collaborations around a focused topic. Each discussion will be led by a facilitator who keeps the discussion on track and the group engaged. To get the most out of this format, please come prepared to share examples from your work, be a part of a collective, problem-solving session, and participate in active idea sharing. Please visit the Interactive Breakout Discussions page on the conference website for a complete listing of topics and descriptions.
Integrated and Continuous Processing
Lara Fernandez-Cerezo, PhD, Associate Principal Scientist, Merck Sharp Dohme (MSD)
- Implementing advanced control process technologies to continuous processes
- Beyond monoclonal antibodies (mAb): applying continuous manufacturing to a diversified pipeline
- Breaking barriers to enhance adoption of continuous manufacturing: how?
Sustainability in Biomanufacturing
- Explore the main environmental concerns in biomanufacturing such as water use, plastics, and energy consumption
- Examine a structured framework that guides organizations in enhancing their sustainability practices
- Discuss specific measures that can be implemented by manufacturing facilities to minimize their environmental impact
- Critical environmental challenges in biomanufacturing and innovative solutions to address them
18:30Close of Day
3月20日(木)
08:00Registration and Morning Coffee
SUSTAINABILITY IN BIOMANUFACTURING
バイオマニュファクチャリングの持続可能性
Minimising the Environment Impact of Biomanufacturing
This presentation will focus on the opportunities we have to understand and progressively minimise the environmental impact of biomanufacturing-highlighting hotspots of concern across the value chain including water, plastics, and energy use. We will showcase the BioPhorum maturity model which provides organisations with a guide to improving their sustainability maturity, highlighting specific actions manufacturing operations can take.
Use of Digital Models to Predict and Optimise Process Economic and Sustainability in Early Process Development
Yuki Abe, PhD, Senior Bioprocess Consultant, BioPharm Services Ltd
Around 80% of costs and environmental impacts are set early in development. New digital process facility models can now predict the Cost of Goods and CO2e emissions at this stage. These models evaluate different technologies and methods, understand trade-offs, and optimize downstream processes to cut costs and reduce environmental impact, thereby maximising benefits. Assessments of different DSP intensification approaches are used to illustrate these models' utility.
Green Metrics to Guide Process Development towards More Sustainable Production of Biologics
Felix Dieringer, Scientist, Takeda, PhD Student, BOKU University
In this talk we will delve into the topic of green metrics to measure and improve sustainability of biologics. In early development, emphasis is typically placed on mass-based metrics, whereas in commercial production the focus often shifts to carbon footprint. How do we address the challenge of finding suitable metrics that are simple to calculate yet effectively predict commercial emissions? How can software like BioSolve help?
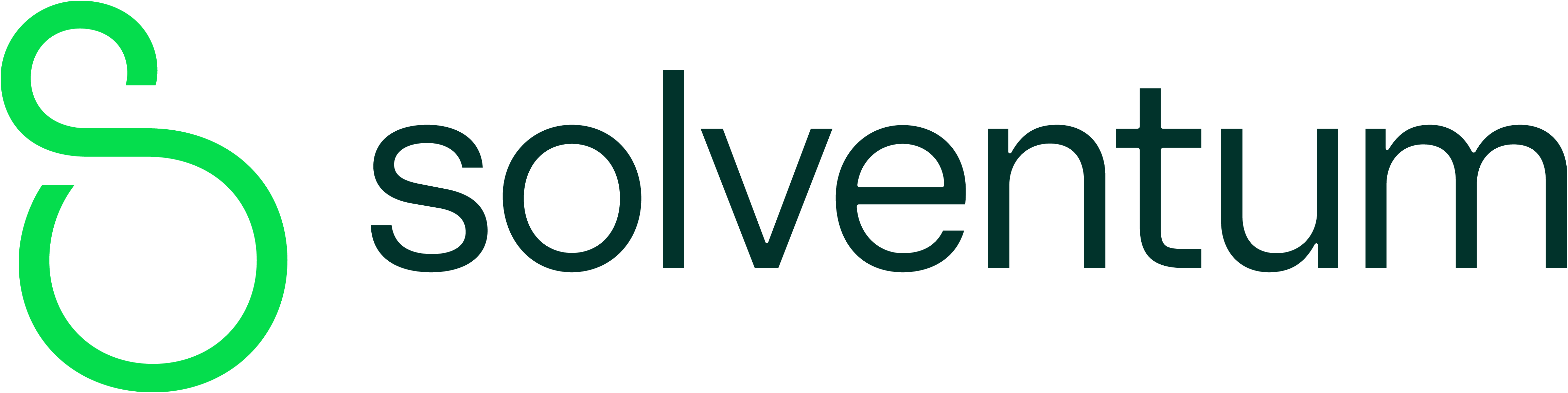
Catherine Bineau, Senior Bioprocessing Applications Specialist, Purification & Filtration, Solventum
The intensification of modern bioprocesses poses challenges at scale. A novel chromatographic technology can be deployed as a clarification platform providing process compression, robustness, and overall efficiency. Sanofi will show how this platform can offer seamless implementation of chromatographic clarification from lab scale to large scale manufacturing, providing process simplification and consistent high quality clarified fluid, thus enabling speed to market. The environmental impact of this platform will be studied through various comparative indexes.
10:30Coffee Break in the Exhibit Hall with Poster Viewing

CONTINUOUS PROCESSING OF MICROBIAL SYSTEMS
微生物系の連続処理
Continuous Processing of E. coli
Gerald Striedner, PhD, Head, Institute of Bioprocess Science and Engineering, Professor, Biotechnology, University of Natural Resources and Life Sciences Vienna (BOKU), Austria
Genome-integrated, as well as growth-decoupled E. coli expression systems, enable continuous protein production. Efficient implementation requires suitable process strategies for cultivation, and product recovery and purification. The presentation will show two case studies inclusive of an economic evaluation with standard fed-batch as benchmark. We will also present results from a cutting-edge, highly-funded, innovative R&D project named ECOnti.
ECOnti-Accelerated, Low Ecological Footprint, Manufacturing Platform for Continuous Production of Biotechnological Products
Juergen Mairhofer, CEO & Co-Founder, enGenes Biotech GmbH
The ECOnti consortium was created to advance continuous manufacturing using Escherichia coli (E. coli) with a capacity of up to 10 litres per batch. By leveraging advanced model predictive control and conducting detailed economic modelling, our goal is to elucidate the cost-effectiveness of continuous manufacturing frameworks as opposed to conventional batch-based approaches.
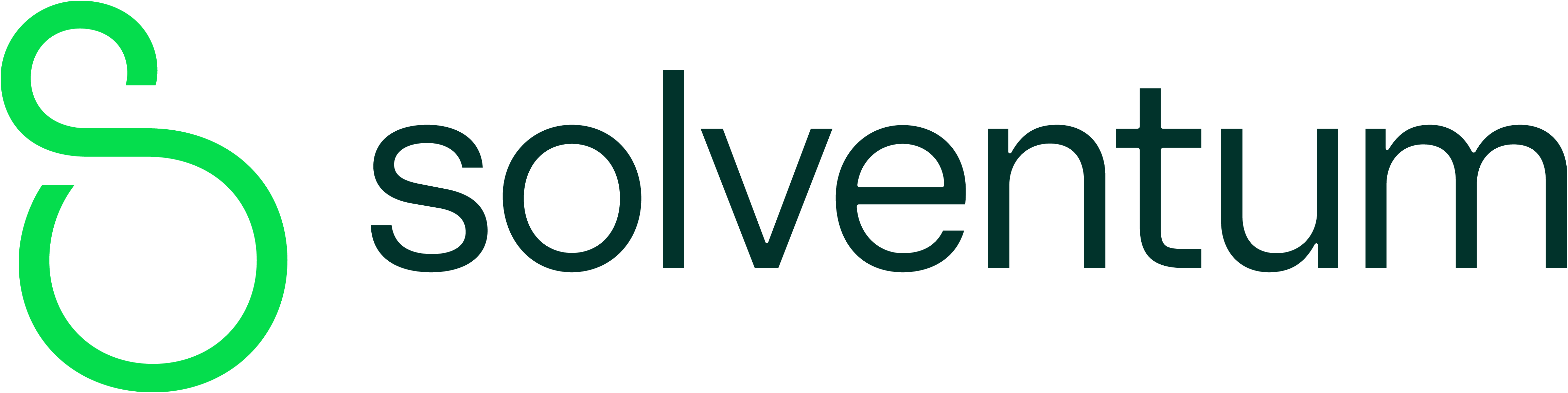
Dr. (Ph.D.) Jack Cordrey, Sr Bioprocessing Applications Specialist, Purification & Filtration, Solventum
Biosimilars offer life-saving therapeutics at fractional costs through streamlined process development. Our case study achieves simplified and intensified single-step clarification using 3M Harvest RC Chromatographic Clarifier, removing of key process-related impurities, including up to 4 LRV for DNA/ chromatin and 50% reduction for host cell proteins. High throughputs >100L/m2, and recoveries >90%, the achieved Cost of Goods are reduced, envisioning faster and linearised process scale-up.
12:40Networking Lunch in the Exhibit Hall with Poster Viewing

Hybrid Modelling Enables Autonomous, Fully Continuous Bioprocesses
Benedikt Haslinger, Bioprocess Modelling Engineer, Novasign
An innovative approach for integrated, continuous protein production will be presented, focusing on dynamic process modelling and simulation. By utilising physics-informed machine learning, we explore the possibilities of characterisation, optimisation, and predictive control of a bioprocess chain involving a two-stage bioreactor system in combination with membrane filtration and multi-column chromatography (MCC). These findings extend their impact to a multitude of industries, including pharmaceuticals, industrial enzymes, and cultured meat production.
CONTINUOUS PROCESSING OF VLPs, mRNA , pDNA
VLP、mRNA、pDNAの連続処理
Continuous Processing of Non-Enveloped Virus-Like Particles
Lukas Gerstweiler, PhD, Lecturer, School of Chemical Engineering, The University of Adelaide
Virus-like particles (VLPs) are highly efficient vaccines and possible drug delivery vehicles. Their purification is challenging with low recoveries, making them relatively expensive. This presentation outlines the main challenges during downstream processing and basic design and process principles for continuous and integrated purification of non-enveloped VLPs that can be used as vaccines.
Development of an Integrated Continuous Precipitation-Based Process for mRNA Purification
Carme Pons Royo, PhD, Postdoctoral Associate, Massachusetts Institute of Technology
mRNA-based therapeutics have emerged as cutting-edge technologies for treating various diseases. Current downstream processing, which relies on a series of chromatography methods and TFF, remains challenging with low yields and significantly impacted final production costs. We will present our integrated and continuous manufacturing process for mRNA production and purification. We are investigating novel methods for continuous mRNA precipitation-based purification, including various precipitating agents, and following precipitation with continuous flow filtration.
15:00Close of Summit
* 不測の事態により、事前の予告なしにプログラムが変更される場合があります。
アジェンダ・講演者・スポンサー更新